The reservoir bodies on all our pumps are made from a rigid, high-strength, transparent plastic that offers high heat resistance and performs well in a broad temperature range. It’s called Polysulfone, and because it also retains its mechanical properties when exposed to steam, grease, solvents and chemicals, it’s also regularly used in the manufacturing of medical instruments, food and beverage processing machinery, aircraft instrumentation, and even motorcycle visors.
As with all plastics, manufacturing with polysulfone involves injection molding, the process of heating the material until it’s hot enough to flow, and then injecting it into a mold through a small opening called a "gate." Once it’s ejected from the mold, a small lump of plastic usually remains attached to the gate that gets trimmed away by hand. In the case of our reservoir bodies, some have more material removed than others which creates the appearance below.
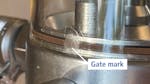
Gate marks are not cracks. They are a normal part of the manufacturing process. Most gates leave a vestige that is barely noticeable, but because polysulfone is hard and clear, the gates can be more visible than with opaque plastics. This is strictly visual. We inspect all reservoir bodies during assembly to ensure there are no defects that will impact the ability of the pump to retain hydraulic fluid or to generate pressure. We also leak-test all pumps during production.
Because these visual inclusions are present to some extent on all reservoir bodies, there is no need for replacement. However, if any pumps are found to be leaking hydraulic fluid from the reservoir, either at the top or the bottom; or failing to generate pressure, this should be brought to the attention of Ralston Instruments and we will determine an appropriate solution.