Analog pressure gauges are very common in industrial installations — they’ve been around for over 170 years. There are several reasons for analog pressure gauges’ popularity, including that they are relatively inexpensive, they don’t require electricity, and they can be readily used outdoors and in hazardous locations. In particular, they can be well suited for less critical applications that may only need pressure readings at infrequent time intervals.
But how pressure gauges are now used is quickly evolving as industrial processes become more sophisticated, more precise, and more demanding. The following article helps you compare analog vs. digital pressure gauges for your application’s specific needs.
How Analog & Digital Pressure Gauges Work
As you consider your application, it’s good to understand the basic technologies of both types of pressure gauges.
Analog or “mechanical” pressure gauges (also called “pressure meters”) all rely on precision mechanical linkages. The most common analog pressure gauge technology uses a Bourdon tube (invented in 1849), where pressure moves — slightly uncoils — a curved tube. The Bourdon tube is, in turn, connected to a series of linkages, gears, and a hairspring that moves the gauge’s dial (pointer). The other two analog gauge sensing technologies — diaphragm (aka “membrane”) and bellows — also depend on very precise mechanical linkages.
With digital pressure gauges, there are no moving parts. A sensor measures pressure variations and converts them into proportional electrical signals. An integrated microprocessor then converts those electrical signals into numeric values, which are shown on the gauge’s digital display.
Laboratory Accuracy vs. Real-World, In-The-Field Accuracy
As most pressure gauge users already know, “accuracy” is not always a simple comparison of percentages. There are different types of accuracy specifications: percentage “of full scale,” percentage “of reading,” combined percentage “of reading” and percentage of “full scale,” and percentage “of span.” One type of accuracy isn’t better than another; it comes down to how the gauge will be used over an anticipated range of pressures.
But if we’re comparing, for example, two pressure gauges — one analog and one digital — with the same laboratory accuracy specifications (say, 0.1% of full scale) and the same pressure ranges (e.g., 0 to 1000 psi), then we can meaningfully compare how the two technologies differ when used in the field. For example:
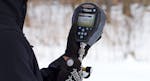
#1 Vulnerability to Extreme Temperatures: High or low temperatures can severely affect the accuracy of analog pressure gauges. (Think of all of those mechanical linkages, thermally expanding or contracting.)
On the other hand, when given the expected high and low temperatures of a given application, manufacturers of quality digital pressure gauges can electronically compensate (or “characterize”) the device to accurately work from -20°C to +50°C.
#2 Pressure Pulsations & Wear: Continual rapid pressure pulsations cause the precision mechanical linkages of an analog pressure gauge to wear out over time, making it impossible to keep the gauge in calibration.
With no moving parts, pulsations are much less of a concern for digital pressure gauges.
Repeatability: The Key To Accurate Pressure Readings
“Repeatability conditions,” as defined by ISO.org, include the same measurement or test procedure, done by the same operator, using the same measuring or test equipment, in the same conditions and location, done repetitively over a short period of time. Some basic considerations regarding repeatability and pressure gauges include the following:
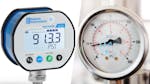
#3 Analog’s “Parallax Effect”: Analog gauges are often misread — they are meant to be read exactly perpendicular to the dial face. The angle dependency of analog pressure gauges is known as the “parallax effect.” Readings taken at other than 90° to the dial could potentially impact accuracy more than the accuracy rating of the gauge. Parallax problems are further compounded when gauges are in hard-to-reach locations.
Angle dependency (parallax) isn’t an issue for digital pressure gauges — the numeric values shown don’t change based on the user’s position.
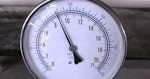
#4 Analog Requires Interpretation: When we look at an analog dial, we’re interpreting where the pointer lies, trying to visually align it with hash marks and then mentally counting or estimating the hash marks between major designators. For example, the pointer on this 0 to 1000 psi analog gauge is about two thirds of the way between 400 and 450 psi, which is (quick!) what value? In this case, the reading is further compromised by the distortion caused by the liquid-filled face.
Using the same example as above, under the best-case scenario you’re interpreting where the pointer lies with a plus or minus of a hash mark, which in this situation is ±10 psi. With digital pressure gauges, there’s no interpretation — just digits to read: 433.3 psi.
#5 Poor Lighting: The ability to accurately read an analog gauge — that is, the location of its dial and the appropriate hash marks — is diminished by poor lighting and shadows.
Conversely, digital pressure gauges can display their readings in large, clear, backlit numbers in a pitch-black location.
#6 The Effects Of Constant Pulsation On Gauge Readability: On analog gauges, continual pressure pulsations can make accurate pressure readings difficult or impossible because the needle is rapidly bouncing around so much. The dial face can be filled with liquids like glycerin to try to somewhat “dampen” the bouncing, but the liquid can interfere with readability — e.g., causing distortions — and any leaks are very messy to deal with.
Digital pressure gauges, on the other hand, can be digitally dampened to adjust their presentation rate of the pressure values. For example, on Ralston LC pressure gauges, you can change the refresh rate from slow to fast, making even precise values easy for a technician to read.
Pressure Gauges & Application Versatility
#7 More Precise Leak Detection: The increased readability of presented values — and, subsequently, the more accurate user readings — of digital pressure gauges provides more precise results when testing for small leaks than analog gauges.
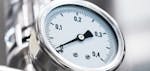
#8 (Small) Size Matters: For analog pressure gauges to truly deliver highly precise (e.g., 0.1% FS) accuracy over a large pressure range (e.g., 0 to 1000 PSI), the size of its dial must become quite large. This can be a problem for space-restricted installations or when the gauge is being used as a calibrator for other pressure gauges. With a technician carrying around multiple gauges for different pressure ranges, their toolbox can become crowded with large analog devices.
By comparison, digital pressure gauges are much more compact. They’re also less vulnerable to shocks while being carried around in a toolbox.
Increased Data Availability & Useability from Your Pressure Gauges
#9 Multiple Engineering Units: Unless they have a double set of hash marks, analog pressure gauges can provide only one set of engineering (measurement) units, e.g., either PSI or Bar or kPa, etc.
Due to the flexibility of their microprocessors, digital pressure gauges have no such limitation: they can provide as many as 15 different engineering units that the user can scroll through by simply pushing a button on the gauge. More sophisticated digital pressure gauges connect to software that allows the user to select only the units they need. Some digital gauges even give you the ability to use your own custom engineering units, such as displaying pressure in torque or force units.
#10 Storing Measurements: Analog pressure meters with additional “follower” pointers can record high and low pressure events, but these recordings are approximate and the pointers are difficult to reset.
Many digital pressure gauges, on the other hand, can accurately record maximum and minimum pressure values, which are stored in the gauge until cleared by the user. Digital meters can also record pressure spikes, which is beyond the capability of most analog pressure meters.
#11 Remote Sensing/Data Logging/Control Interconnects: Digital gauges will be your choice if you want to use USB, Bluetooth(™), Zigbee(™), or other communication protocols to remotely monitor and record pressure, in addition to reading the gauge where it’s located.
Durability & Vulnerability
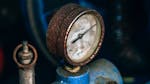
#12 Typical Pressure Gauge Vulnerabilities
Typical damage to analog pressure gauges include:
• Broken windows and damaged pointers
• Leaks (glycerin) coming from the gauge’s face
• Discolored liquid in the gauge’s window
Typical damage to digital pressure gauges include:
• Punctured displays
• Damage to the faceplate/keypad
That said, quality digital pressure meters are made from study materials, such as — aluminum or stainless steel — with thick, crack-resistant plastic faces that offer substantial protection from hazardous chemicals, drops, shocks, and flying debris.
Verification, Recalibration & How Often Gauges Go Out-Of-Calibration
Both types of pressure gauges are verified using the same steps: connecting the gauge to a well-regulated pressure supply and running a series of testing steps to verify that the gauge is within calibration. One significant difference is that the analog gauge must be verified in its installed position (orientation), which can make the verification awkward to perform; there is no such requirement for pressure gauges.
#13 Recalibrating A Gauge: If an analog gauge is found to be out-of-calibration, it will probably need to be moved to the more controlled environment of the maintenance shop for steps such as removing the window, adjusting screws on the dial or screws on the pointer itself, internal inspection, cleaning, and possibly the disassembly and reassembly of the precision mechanical linkages. Given these complications, the potential for errors, and the cost of skilled plant technicians, “problem” analog gauges are frequently just thrown away and replaced with new gauges.
By comparison, recalibrating a digital pressure gauge can be simple and fast. Here’s an example using the Ralston LC Series: while the gauge is still connected to the well-regulated pressure supply, the technician connects a USB cable to the gauge and uses software for the 3-point recalibration process. In most cases, it literally takes just a few minutes.
#14 How Often Gauges Go Out-Of-Calibration: The precision mechanical linkages used by analog pressure gauges makes the linkages vulnerable to being loosened or moved out of position (and, therefore, the gauge out-of-calibration) by the vibrations, shocks, and overpressure typical in industrial applications. Even the act of shipping a well-packaged analog gauge can, for example, take an analog pressure gauge out-of-tolerance.
By comparison, quality digital pressure gauges can withstand significant vibrations, shocks and overpressure without losing their calibration due to their solid state design.
Therefore — and this is a key point — digital pressure gauges stay calibrated much more reliably than analog pressure gauges.
Pressure Gauge Costs & Power Requirements
Comparing Costs — Analog vs. Digital Pressure Gauges: When comparing quality pressure gauges, digital gauges can be several times the cost of analog gauges.
But for all the reasons listed in this article, buying an analog gauge could be “false economy” based on your intended use. Reliable (and highly readable) pressure readings not only keep your production online, they also keep your employees safe. And rather than constantly calibrating analog gauges, digital pressure gauges free up your maintenance people for higher-value activities.
Power: Digital pressure gauges require electricity, whether that is from common batteries (e.g., AA alkaline), loop, or solar. For reference gauges, this really isn’t too much of an issue: you just put a set of new, spare batteries in your tool bag. For process pressure gauges, hardwired to power and installed in a panel, you might want to leverage the gauges’ connectivity as well — running your data line parallel with the 120/240 VAC line.
A Quick Summary of Analog vs. Digital Pressure Gauges
Getting Started with Digital Pressure Gauges
The pressure calibration specialists at Ralston Instruments offer three series of robust digital pressure gauges, suitable for measuring the pressure of air, alcohol, antifreeze, ethylene glycol, hydraulic oil, inert gas, mineral oil, natural gas, petroleum based oil, Skydrol, windshield washer fluid, transmission fluid, light motor oil, Ralston calibration oil, and water.
Two of the LC Series, the portable LC10 and the LC20 are specifically designed as field (reference) calibrators of other gauges, while the LC30 is a process meter meant for panel mounting. To learn more, visit Ralston Digital Pressure Gauges.
Attribute | Analog Pressure Gauges | Digital Pressure Gauges |
---|---|---|
Easy, screw-in installation | $ | $$ - $$$ |
Cost of gauge | One | One |
Requires power – battery, loop or solar | No | Yes |
“Of reading” accuracy | Smaller range | Wider range |
Temperature extremes affect accuracy | Yes | Can be temperature compensated for anticipated range |
Overall reliability | Lower | Higher |
Resistance to wear from constant pulsation | Lower | Much higher |
Resistance to over-pressure spikes | Lower | Higher |
Resistance to most chemicals | Good | Good |
Must calibrate in position (orientation) used | Yes | No |
Steady reading during high vibrations, pulsations & rapid pressure changes | No (even with glycerin) | Yes, can set presentation rate to several seconds |
Can record pressure spikes | Rarely available (?) | Readily available |
Memory of measurements | No | Readily available |
More than 2 engineering units | No | Readily available |
Custom engineering units | Requires custom printed dials | Readily available |
Recalibration process | Complicated, slow, and frequently not economical | Simple and fast |
Calibration test frequency | High | Low |